3 Simple Techniques For Alcast Company
Table of Contents4 Easy Facts About Alcast Company DescribedTop Guidelines Of Alcast CompanyThe 5-Second Trick For Alcast CompanyOur Alcast Company PDFsOur Alcast Company PDFsHow Alcast Company can Save You Time, Stress, and Money.The Of Alcast Company
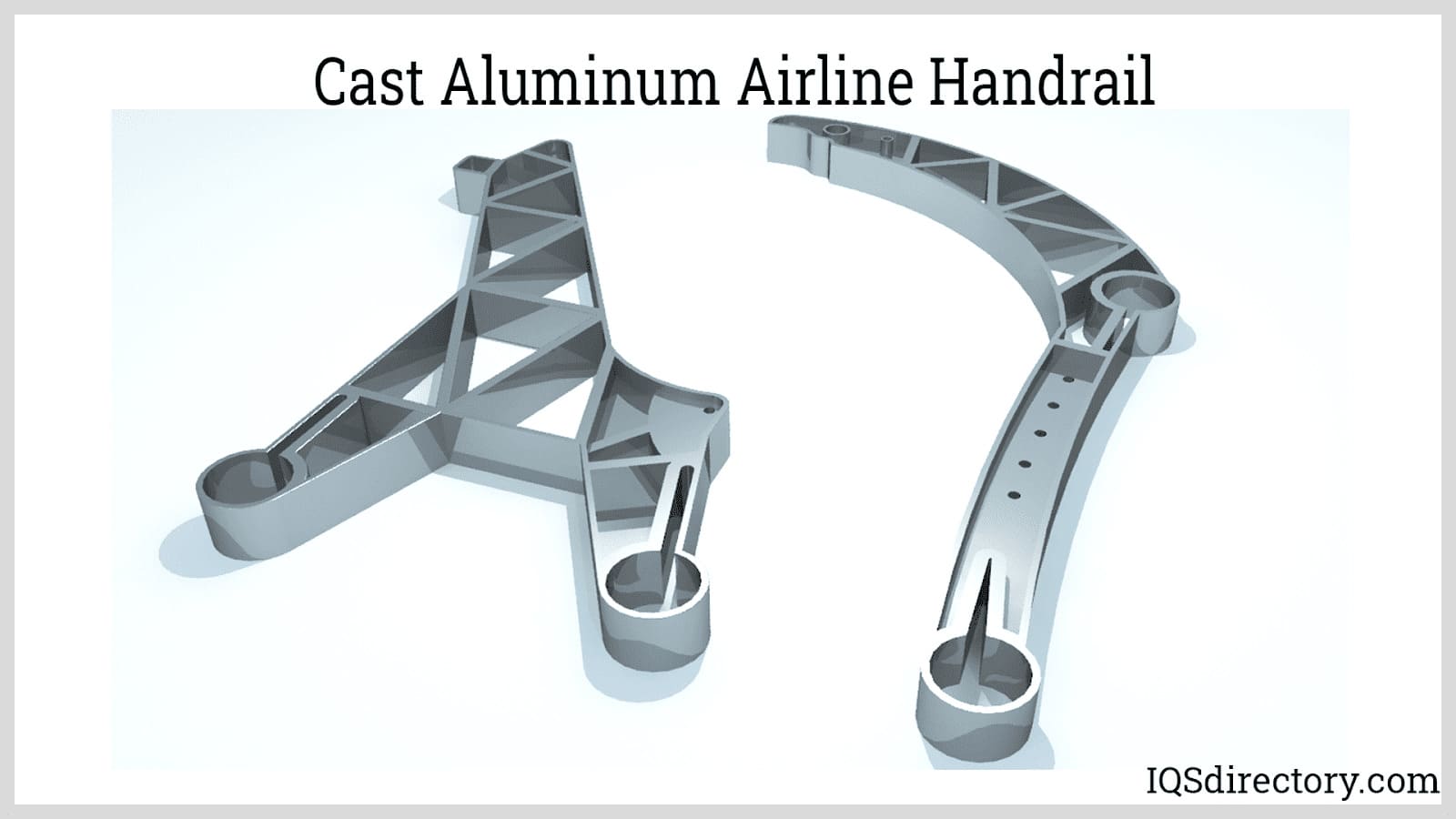
If you believe that a wrought alloy might be the finest for your task, take a look at several of our articles that clarify even more about specific functioned alloys, such as Alloy 6061 and Alloy 6063. On the various other hand, if you believe an actors alloy would certainly be much better for you, you can discover more about some cast alloys in our Alloy 380 and Alloy 383 short articles (coming quickly).
Unknown Facts About Alcast Company
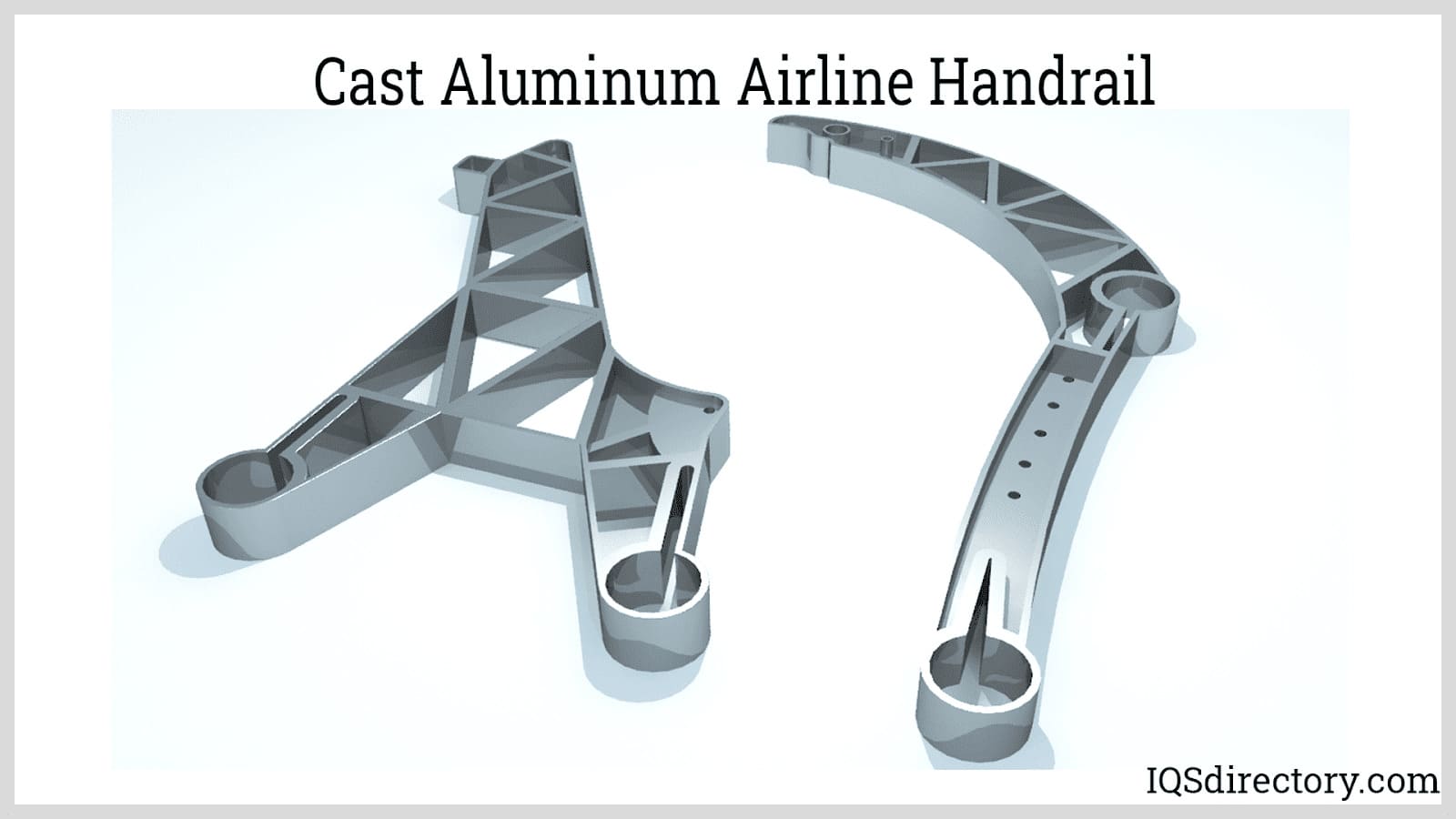
Having the experience and sector knowledge to craft your spreadings for optimal manufacturing and high quality results will simplify the job. Making aluminum spreading needs a complex collection of processes to accomplish the ideal results. When choosing a brand-new light weight aluminum factory to companion with, ensure they have extensive sector experience and are experienced regarding all aspects of the light weight aluminum spreading procedure: style, production, material analysis, and item screening.
(https://www.openstreetmap.org/user/a1castcmpny)The shop ought to also have a tried and tested record of providing remarkable items that satisfy or surpass consumer expectations. Quality control needs to also be at the top of your list when selecting an aluminum shop. By dealing with a qualified factory who complies with the criteria for quality assurance, you can safeguard the honesty of your item and guarantee it satisfies your requirements.
6 Easy Facts About Alcast Company Explained
By choosing a company that uses solutions that meet or exceed your product requirements, you can be certain that your project will be completed with the utmost accuracy and performance. Different components call for various manufacturing strategies to cast light weight aluminum, such as sand spreading or die casting.
Die spreading is the name offered to the process of developing complex metal components through usage of mold and mildews of the component, also recognized as passes away. It produces even more components than any type of various other process, with a high degree of precision and repeatability. There are 3 sub-processes that fall under the group of die spreading: gravity die spreading (or permanent mold casting), low-pressure die casting and high-pressure die casting.
After the pureness of the alloy is evaluated, dies are produced. To prepare the dies for casting, it is essential that the passes away are clean, so that no deposit from previous manufacturings continue to be.
The pure steel, likewise referred to as ingot, is included to the heater and maintained the molten temperature of the steel, which is then transferred to the injection chamber and infused into the die (Aluminum Casting). The pressure is then kept as the metal solidifies. As soon as the steel strengthens, the cooling procedure starts
Alcast Company Things To Know Before You Get This
The thicker the wall surface of the part, the longer the cooling time due to the quantity of interior metal that additionally requires to cool. After the element is totally cooled, published here the die cuts in half open and an ejection mechanism presses the part out. Complying with the ejection, the die is closed for the next injection cycle.
The flash is the extra product that is cast throughout the process. This need to be cut off utilizing a trim device to leave simply the main element. Deburring removes the smaller items, called burrs, after the cutting process. Finally, the element is polished, or burnished, to give it a smooth finish.
Alcast Company Fundamentals Explained
This verified to be an unreliable test, due to the fact that the tester might cut right into an item and miss out on an area with porosity. Today, top manufacturers make use of x-ray screening to see the whole interior of components without cutting right into them. This enables them to much more precisely approve or deny parts. To reach the finished product, there are 3 primary alloys made use of as die casting product to select from: zinc, aluminum and magnesium.
Zinc is among the most pre-owned alloys for die casting due to its reduced cost of raw materials. It's also among the more powerful and stable metals. And also, it has superb electrical and thermal conductivity. Its corrosion resistance likewise enables the components to be lengthy enduring, and it is one of the much more castable alloys due to its lower melting point.
All about Alcast Company
As stated, this alloy is one of one of the most generally made use of, yet manufactures will, sometimes, choose aluminum over zinc as a result of light weight aluminum's production benefits. Aluminum is very affordable and among the extra flexible alloys. Light weight aluminum is used for a number of different products and industries anything from window frameworks to aerospace materials.